Despite pandemic-related jitters, the global manufacturing sector is back again – and growing. Research from Deloitte points to an expansion rate of more than 4% in 2022, with industry players turning would-be weaknesses into competitive advantages by innovating solutions for supply chain challenges and digital technology adoption.
The increasing use of augmented reality (AR) tools by manufacturers is no exception to this. If the factories of the future, as Harvard Business Review wrote in 2018, will run on better processes – and not simply more sophisticated tools – AR is one of the strongest candidates out there. Its adoption can implement real, radical change that boosts worker experiences, drives innovation, and achieves essential improvements in productivity and costs.
Surveying the manufacturing industry landscape
Priorities for manufacturing, both in 2022 and beyond, will involve meeting several challenges with dynamic and responsive solutions:
- The need for supply chain adaptability, with multi-tiered responses to external disruptions.
- A combination of demographic shifts, changing customer expectations, and a skills gap where the expertise needed and the expertise that exists in the workforce are mismatched. The latter means, in particular, that training, upskilling, and reskilling will need to change.
- Increased public attention to companies’ climate impact, with a need for them to show, not tell how they are responding to environmental concerns and decreasing their footprint.
- The complexities of digital technology adoption, with digitization needing to be integrated within as few tools as possible, rather than organized in silos.
For our part, SightCall technology plays a role in several ways. Our AR-powered visual assistance tools minimize slow response and recovery time to disruptions, eliminate the time/cost and carbon impact of wasted dispatches, reduce employee turnover, and prevent proprietary knowledge from being lost.
To gain a fuller picture as to why, read on to understand the role that augmented reality technology can play for manufacturing companies.
What is Augmented Reality in Manufacturing
The complexity of modern technology, diagnostic systems, and computerized interfaces means that technicians now require a higher level of training and certification than their predecessors. Consequently, AR blends the physical and digital world by superimposing images and text onto a user’s view through a device, such as a smartphone or a tablet, and provides an enhanced composite view.
Augmented reality empowers manufacturing workforces and elevates service offerings through better resolution rates, reduced downtime, and improved customer satisfaction.
Using tools with augmented reality features can augment a technician’s skills and knowledge by providing them with all the resources they need to complete tasks including instructions, manuals, and even live support from more senior technicians.
What is AR-powered visual support?
Visual assistance, otherwise known as visual support, connects technicians and experts in a virtual, interactive environment where they can troubleshoot, train and resolve complex work orders with reliable video, augmented reality, and artificial intelligence (AI) insights. AR tools in visual support allow technicians to make on-screen annotations, obtain accurate measurements remotely, and share images and information during the live video session.
With AR, an organization’s most skilled technicians can handle more jobs remotely, giving them the freedom to focus on high-value customers, complex repairs, and supporting technicians in the field.
What are the benefits of Augmented Reality for Manufacturing?
How many failed work orders would be successful if there was an easier way to receive guidance in the field? With visual support, technicians have immediate access to remote experts, ensuring that they are never alone on a service call. From any mobile device or wearable, they can receive live, AR-powered visual assistance to help them resolve complex tasks.
- Customer support: Manufacturing organizations can differentiate themselves with a modern approach to remote customer support. With immediate visual assistance, they can reduce the service wait from days to minutes.
- Technician support: Manufacturing organizations can equip their service teams with one-touch visual assistance through a mobile app or wearable, improving uptime and empowering their technicians to accomplish tasks on the first call.
- Hands-on training: Manufacturing organizations can empower their technicians with the ability to learn new skills on the job. Less experienced technicians and engineers can use visual assistance, AR, and AI to guide them through new repairs and complicated work orders.
- Data-driven maintenance: Using AI-driven insights, manufacturing organizations can make informed decisions by identifying parts, diagnosing issues, and proposing solutions based on data.
Tools such as Smart Optical Character Recognition also help to accurately read and interpret data on a machine. They can identify printer parts with 100% accuracy by simply taking a photo. All information is fed directly back to the case file, speeding up repairs and reducing parts wastage with no manual data entry required.
- Self-guided maintenance: By replacing old paper processes with AR digital processes, field agents can self-guide through a pre-structured set of workflows. SightCall empowers technicians in the field, giving them step-by-step instructions to independently complete a work order.
- Wearables: These digital devices can be worn on the body, embedded or contained within clothing, and even tattooed onto the skin. The leading benefit for companies adopting wearable devices for their workers is straightforward, in that handheld devices are replaced by tools like smart glasses, freeing service experts to use their hands in complex or risky work situations.
According to our internal research, manufacturing companies specifically realize average improvements of:
- 81% in first-time fix rates
- A 69% reduction in time to issue resolution
- 50% reduction in truck rolls
- Knowledge savings through a 41% decrease in training time
- Customer satisfaction, increasing by as much as 30 points
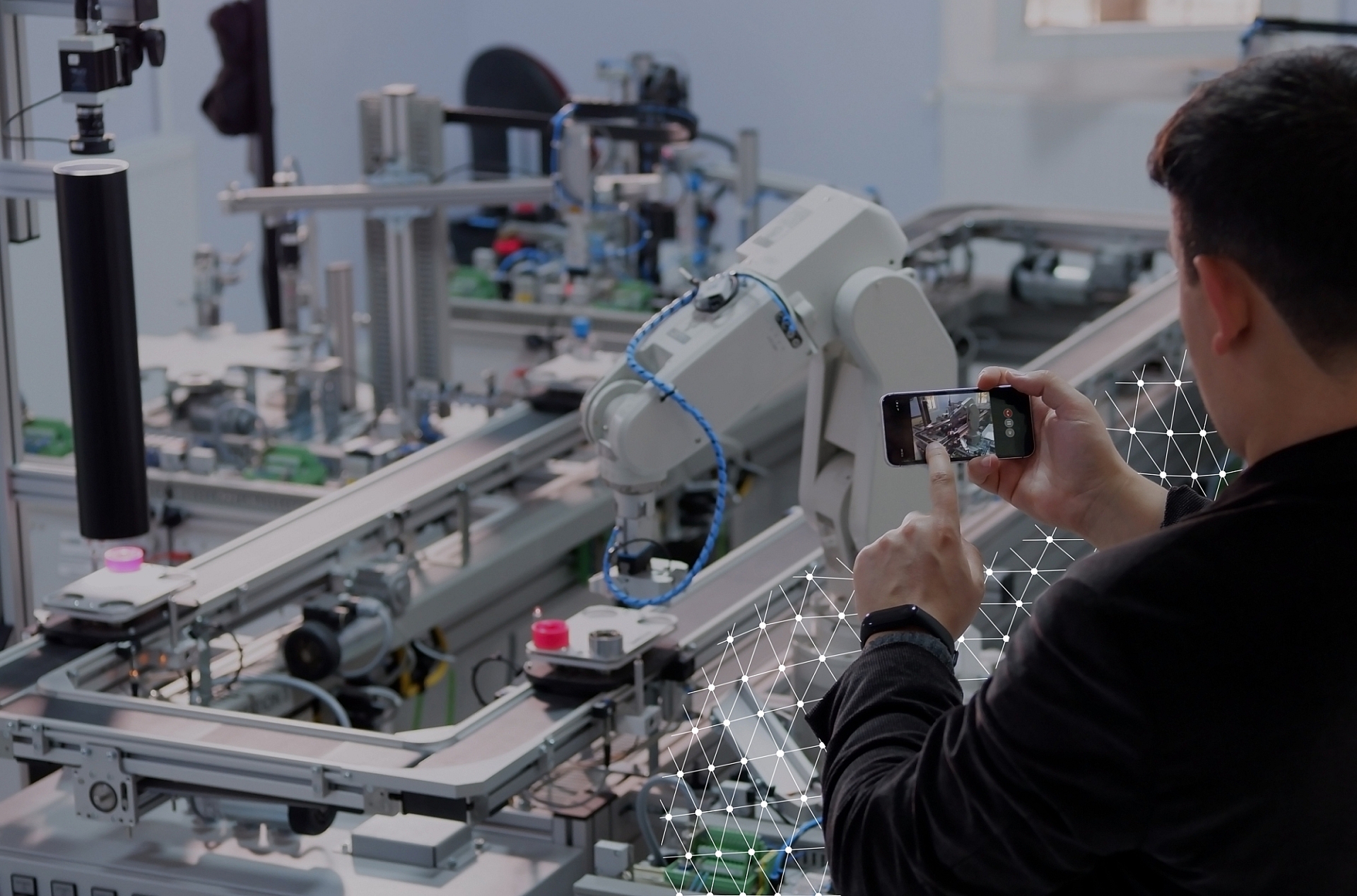
Looking for a visual augmented reality solution for your company?
How can digital process automation improve manufacturing processes?
Digital process automation (DPA) harnesses technology to standardize workflows, improve performance and mitigate errors that traditionally hold essential processes back. Its use entails both self-guided maintenance and human-guided visual assistance.
Rather than replacing any part of the existing service experience, DPA boosts technicians’ work and person-to-person connections with customers.
SightCall’s own Digital Flows solution digitizes manual processes to improve efficiency and reduce error. With the help of standardized, step-by-step guidance, including detailed instructions and checklists, technicians and service workers can complete tasks with no ambiguity or confusion.
The training process also becomes more straightforward, with digital process automation providing new technicians or workers needing to upskill with an immersive and straightforward learning experience, mirroring the field service situations they will encounter on a daily basis.
Augmented Reality in Manufacturing Use Cases
Case Study 1: Remote support transforms printer maintenance
MacDermid Graphics Solutions, a leading global supplier of photopolymer printing solutions based in Atlanta, Georgia, delivers high-quality graphics to customers via a diverse array of packaging products. Its operations span North and South America, as well as several countries in Europe and the Asia-Pacific.
MacDermid is widely known throughout the industry for its excellent customer service. The company provides day-to-day solutions on a variety of maintenance, repair, and process issues around the world.
In recent years, the company has been focused on applying virtual solutions to further improve several key performance indicators (KPIs) on equipment maintenance to bolster customer satisfaction and shorten resolution times.
As with many companies, its interest in these tools increased at the onset of the COVID-19 pandemic. With service technicians’ ability to fulfill maintenance and repair work orders on-site significantly curtailed, MacDermid had to balance keeping people safe while maintaining a hard-won reputation for customer care. As such, it was essential to find a solution that would work on mobile devices but also enabled people to use wearable gadgets like smart glasses.
A primary objective was to permit technicians to be remotely guided through a task or repair process with the benefit of AR overlay, while still having both hands able to maneuver.
Customers and technicians can launch SightCall remote support sessions through their own smartphones, providing and receiving crucial work order information in real-time, thanks to an integration with Salesforce.
Even in low-bandwidth environments, sessions benefit from guaranteed HD picture quality and reliable video. And tools like optical character recognition (OCR) can accurately read and interpret data on a machine, even from several feet away, and feed it directly back to the work order, with no manual entry required.
When technicians have no other choice but to go on-site, they can have their hands free to do the work using smart glasses, while a remote expert walks them through it. Because of this, only a single tech needs to be dispatched to handle more complicated cases. The training of junior or less experienced workers has also been boosted by the immersive experience of the platform.
After only a few months of deploying remote support, MacDermid Graphics Solutions realized a 20% truck roll reduction in the number of work orders that required sending a technician on-site. Customers were also guided through issues with their printers with the help of a remote expert, increasing first-time fix rates.
Case study 2: Food safety revolutionized with remote virtual audits
Safe food practices impact consumers all over the world and are crucial for human health. As such, verification involves a complex, multi-level system of inspections and audits, ones which Kraft Heinz uses to ensure quality assurance, identify and coordinate improvements, and resolve issues related to customer complaints.
Despite the COVID-19 crisis and the travel restrictions that came with it, Kraft Heinz needed to continue the high standards of food safety for consumers, without disrupting a supply chain built on a wide network of suppliers, copackers, and warehouses.
The company required a remote virtual support system robust enough to be implemented in a variety of specific use cases, and allow for the standardization of both routine and incident-related audits. Deploying visual assistance in just weeks, Kraft Heinz leveraged SightCall for every step of their visits to their partners, including suppliers, copackers, factories, and warehouses.
Before inspections begin, sessions are used to share relevant documents and arrange logistics. During the inspection, expert remote auditors deploy features like flashlight control to obtain better visibility in dim light, and augmented reality (AR) annotations to illustrate recommendations or identify potential problems. With the ability to capture and save photos from live video they can store visual records of equipment and processes alongside the inspection or audit documents.
Previously, visits such as factory tours and inspections could take up to three days, entailing multiple visits. This was due to the requirement of reviewing relevant documents and certifications while on-site – something that can now be done with virtual inspections in advance.
With less travel, simple coordination, quicker resolution times, and the ease of storing documentation, the number of inspections and audits conducted has skyrocketed – with the added benefit of a socially conscious company with a lower carbon footprint.
Case Study 3: An international engineering and service company
Note: Some of our clients prefer to remain anonymous while sharing their achievements.
This client is an international engineering and service company employing over 60,000 personnel with 20,000 field engineers across 60 countries worldwide. It builds and services moving walkways, automatic doors, gates, escalators, and lifts. Committed to modernizing infrastructure in urban spaces, it has recently invested in new technologies like touchless building components and antimicrobial surfaces.
Five years ago, this company launched a technical help desk (THD) to assist its technicians with field maintenance. It hoped to reduce the number of times second and third field techs were dispatched to a job site to troubleshoot an issue. It instead wanted technicians who were in training to call the THD and speak remotely with an expert when problems arose.
If a solution could not be reached over the phone, a video call could be launched through the Salesforce platform. Of about 200 THD inquiries per day, the company estimated that between 8% and 10% used video calls, typically the most complex or challenging cases. The previous remote assistance supplier led to problems such as extensive setup time, limited Salesforce integration, and mixed user experience feedback.
The client was eager to transition to a solution that also allowed the seamless integration of data collection in real-time with Salesforce. Integrated global data could then be analyzed to refine remote assistance processes, targeting situations and business areas needing improvement and driving greater operational efficiency.
The client chose SightCall for its virtual assistance needs, attracted to its ease of integration with Salesforce. The company transitioned its 700 THD agents onto the platform within a matter of days and with zero interruptions.
Once the need for a video call was determined case-by-case, an agent could assist technicians remotely through AR and AI tools. The calls were launched from within the technician’s Salesforce console on their phone, without any need for additional apps or tools.
With SightCall’s advanced AR capabilities, agents harnessed tools like remote activation of the smartphone camera to illuminate dark spaces, direct annotation of items of interest by drawing or marking on the screen, and Smart Optical Character Recognition capturing text, barcode or QR codes for immediate transfer.
Because the data from each session is instantly fed back to the Salesforce work order, with little to no button-clicking or manual syncing required, the client was also able to realize its goal of collecting information across different job types and curating it in a central database for strategic use.
Within six months of deploying SightCall, the client saw a 19% decrease in its technician callout rate and a 50% increase in first-time fix rates, which now exceed 80%.
For a company committed to improving its carbon footprint, the reduction in truck trips also created what one of its IoT architects called “a huge leap forward.”
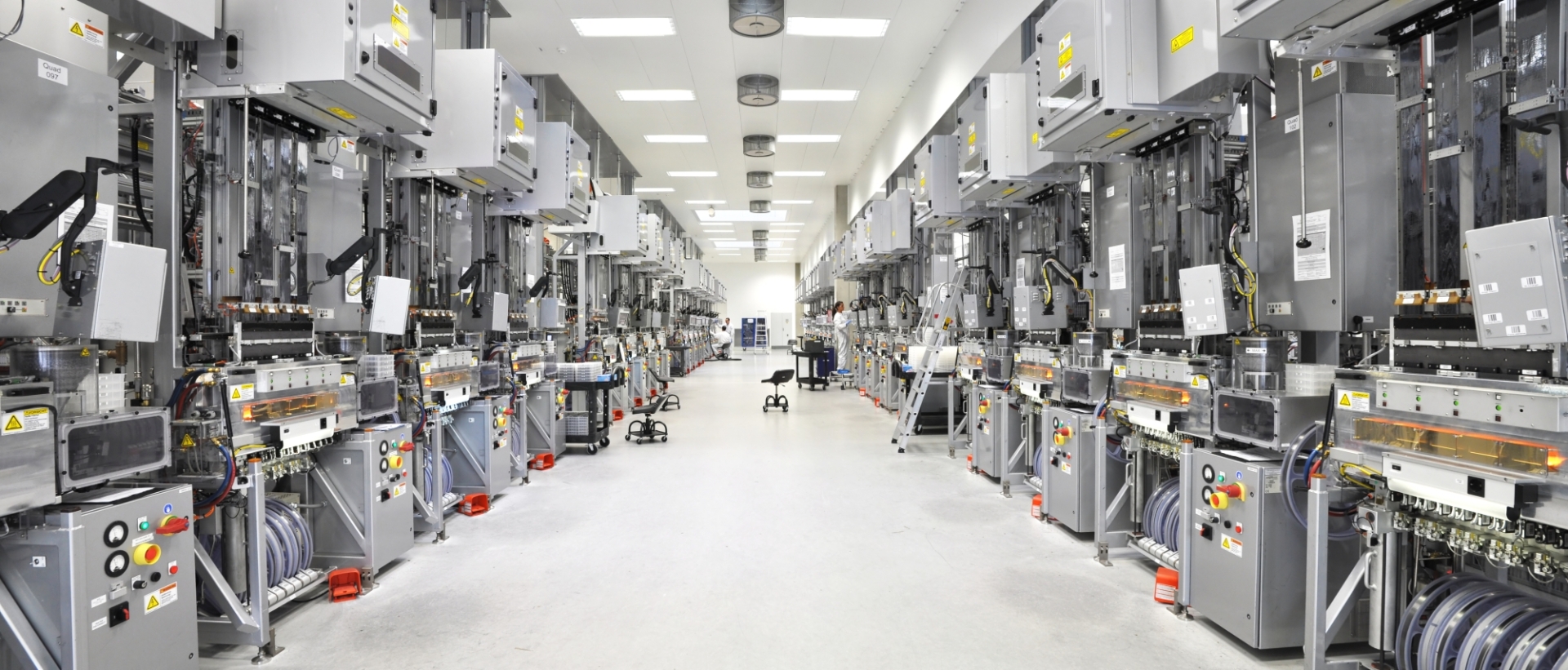
Transform Your Service Organization
Using AR-powered visual support, your organization’s most skilled technicians can handle more jobs remotely, giving them the freedom to focus on high-value customers, complex repairs, and supporting technicians in the field.
SightCall’s enterprise-grade visual support platform harnesses the power of AR to allow technicians to work at their maximum potential, regardless of their experience level or expertise.