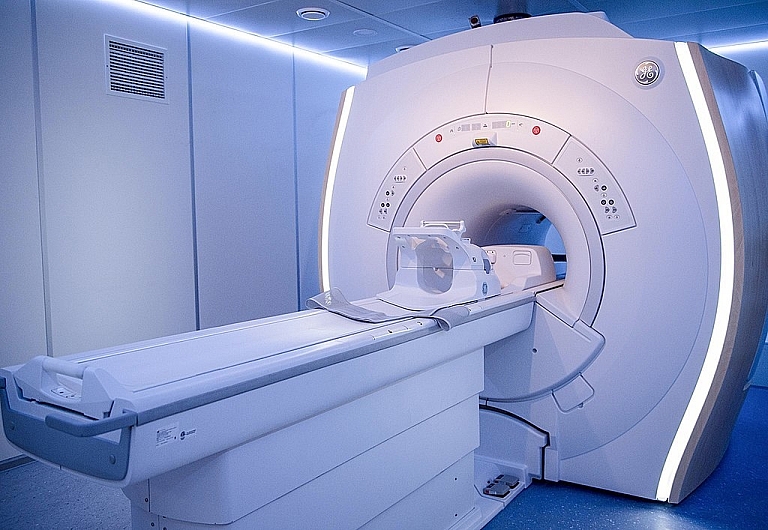
GE Healthcare uses SightCall’s visual support to help technicians diagnose and fix medical equipment issues remotely, reducing downtime and service costs. This allows hospitals and clinics to keep critical devices running with fewer delays.
The Client
GE Healthcare is a global health technology company specializing in the engineering and production of diagnostic machinery – including MRI, CT and X-ray scanners – and offers expert technical services to hospitals, clinics and medical offices to provide post-sales service contracts.
Driven by a mission to create and enable solutions that improve the delivery of healthcare to patients worldwide, GE Healthcare has invested heavily in automated medical appliances, such as artificial intelligence (AI)-driven Critical Care Suites, image-guided surgical tools and predictive protocol ventilators for intensive care patients.
GE is constantly investigating innovative solutions with the goal of enhancing patient experiences and providing immediate repairs in order to put hospitals back on the path to what they did best: saving lives.
The Challenge
When troubleshooting an issue during a field maintenance visit was especially complicated, a field technician frequently mobilized one of their peers or a more senior technician to the job site, resulting in multiple trips and greater labor costs applied to a work order. This often caused the affected machinery to be out of use for a period of time while a solution was found, much to a clinician’s detriment.
From the standpoint of a radiology clinic or a specialist’s office, a day – let alone longer – without an MRI scanner creates a significant functional barrier. Patient appointments have to be delayed or canceled, and the scanner becomes unavailable in the event an emergency arises. GE needed to reduce any unnecessary downtime and ensure the equipment would be available in the moments that matter.
GE Healthcare’s goal was to shorten the length of time on-site and improve first-time fix rates, reducing the need for multiple trips. When the company decided to search for a visual assistance solution, one priority stood out: the highest possible call quality to facilitate real-time work order completion and a higher issue resolution rate.
The Solution
Today, GE Healthcare complements its field support solution with SightCall, drawn to the ease of scalability.
User profiles in multiple regions were set up on SightCall in a matter of days, and a global collaboration subsequently emerged. From Southeast Asia, GE Healthcare expanded remote service into China, Europe, North America and Latin America, and continues to build its relationship with SightCall through ongoing service expansion into other continents. The company also leveraged SightCall to assist in the maintenance and repair of certain product families, particularly medical imaging and ultrasound machines, where remote-guided repairs were found to be most successful.
Both field technicians and remote experts praised the ease of use and accessible interface SightCall offers. Field technicians were impressed by the reliable video quality and consistent audio and video.
Technicians could carry out remote-guided repairs with greater ease and agility, thanks to touchless capabilities using the device of their choice. Site data, like product serial numbers, could be fed back to the work order through the Smart Optical Character Recognition tool, with the smartphone camera simply held in front of the desired data to read it, with no manual entry required.
“By using SightCall, we ensure that our field teams are partnered directly with our technical experts, making sure they are part of the repair and troubleshooting network every step of the way,” said a service operations manager for Asia, the Middle East and Africa. “We can virtually place a technical expert next to a field engineer on a site by using the interactive video and augmented reality features of this application.”
One key area of concern for the GE support teams was the fact that many of the remote locations have low bandwidth or unreliable network conditions. In these areas, connectivity in hospitals can be exceptionally poor due to facilities being clad in lead to provide a safe environment for patients. However, throughout the testing stage, SightCall demonstrated the highest call success rates, leveraging its proprietary global cloud platform to deliver a consistent service experience. Remote technicians benefited from the ability to immediately share pictures, providing them the support and solutions needed, and could receive video help even in 3G environments.
“SightCall was stable and easily accessible throughout all of these tests,” the service operations manager observed.
The platform’s security capability is also industry focused, delivering HIPAA compliance, which is critical for GE Healthcare to operate in the area. This provides the peace of mind for technicians to collaborate anywhere in the world through the use of the same visual assistance solution.
The Results
Besides happier field technicians and a more interconnected organization, GE Healthcare began to notice an increase in several key performance indicators, most notably with improved resolution rates. Maintenance turnaround times were shortened to averages of six to eight hours, versus three days prior to the implementation of SightCall. With the average call taking only 40 minutes, the company estimates it has saved hundreds of thousands in travel costs.
Research suggests an MRI machine faces an average of 30 to 60 hours a year in downtime. At an average cost of 2,000 USD per scan in the U.S. and one hour per scan, hospitals can easily lose between 60,000 to 120,000 USD per year on a single MRI machine. With callouts now completed in the same day, and equipment back up and running in a matter of hours, GE has realized significant cost savings.
GE Healthcare’s partnership with SightCall revolutionizes the way the company can support its customers, reducing device downtime and helping providers spend more time on improving patients’ lives.