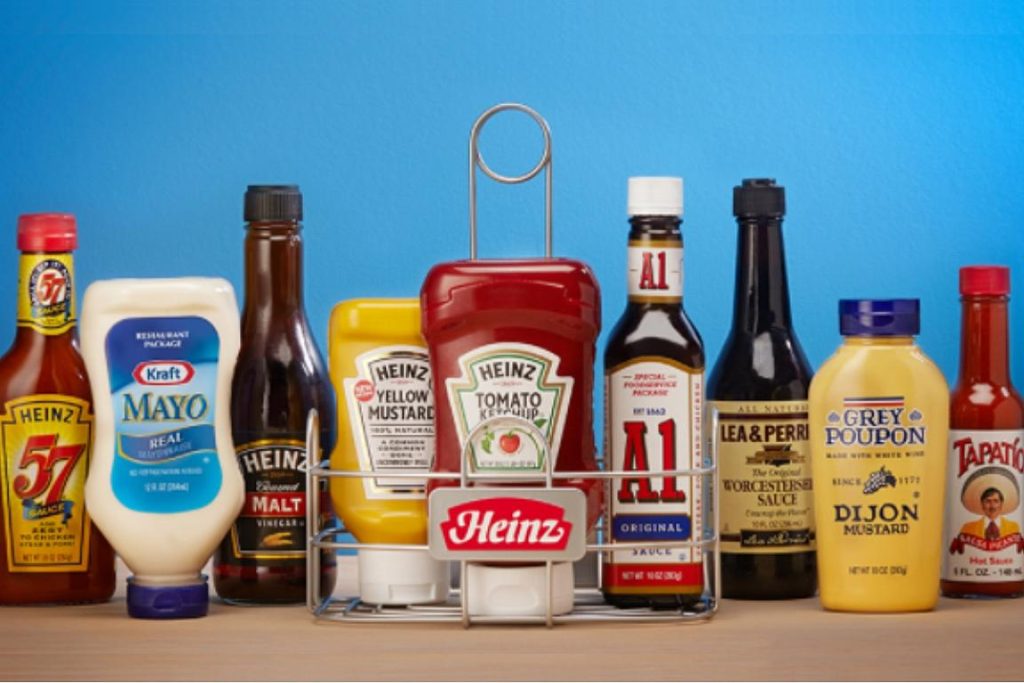
Client
Kraft Heinz is one of the largest food and beverage companies in the world, with sales last year of around $25 billion. Their 38,000 employees support a portfolio of both iconic and emerging brands available in more than 40 countries.
Their vision to create an agile and customer-driven culture has empowered their digital transformation, even as the COVID-19 crisis accelerated their needs for remote solutions.
Challenge
The safety of food practices in compliance with precise regulations and standards is integral to the global food system and human health. While the principles of food safety are straightforward, verification of them involves a complex system of inspections and audits at every level. These inspections are crucial for Kraft Heinz to ensure quality assurance, identify and coordinate improvements, and resolve issues related to customer complaints.
Ensuring the safety of their essential workers during the COVID-19 crisis was paramount. With travel restrictions in place both internationally and between states, Kraft Heinz needed a way to empower their specialists to continue maintaining the high standards of food safety for consumers without disrupting a supply chain built on a wide network of suppliers, copackers, and warehouses.
Kraft Heinz quickly began searching for a remote virtual support system robust enough to be implemented in a variety of very specific use cases and allow for the standardization of both routine and incident-related audits.
Security of information was paramount, as was the need to be able to share and store documents within a single platform. Consistent video quality was also a priority, with some facilities in areas that might have low bandwidth, such as storage warehouses.
Solution
To help Kraft Heinz immediately address the essential safety of their employees as well as consumers around the world, SightCall deployed their visual assistance platform within weeks. Kraft Heinz was able to quickly fold it into their processes for auditing, inspections, document review, and factory tours that had previously only been conducted face-to-face.
Kraft Heinz leveraged SightCall for every step of their visits to their partners including suppliers, copackers, factories, and warehouses. Before the inspection starts, they use the platform to share relevant documents, arrange the logistics, and explain how someone on-site can join the SightCall session.
During the inspection, remote agents can guide the entire process. The expert remote auditors at Kraft Heinz use features like flashlight control to get better visibility in dim light and AR annotations to illustrate recommendations or identify potential problems. With the ability to capture and save photos from live video they can store visual records of equipment and processes alongside the inspection or audit documents.
SightCall is also used for multidisciplinary calls that can bring several people into one SightCall session. This enables the remote auditors to have additional experts to offer specialized advice before and during the inspections and document reviews. The chat feature allows these participants to interact during the live SightCall session to offer suggestions both to the remote auditor and the on-site contact.
Benefits
The flexibility to use any device partnered with strong security and compliance allowed the client to implement remote visual support quickly across multiple use cases at any of their partners’ facilities.
Since deploying SightCall, Kraft Heinz has found that not only are they able to reduce travel time, but their processes are much more efficient. Previously, visits such as factory tours and inspections could take up to three days and sometimes required multiple visits. This was due in part to the need to review relevant documents and certifications while on-site, something that can now be done via SightCall in advance.
With less travel, simple coordination, quicker resolution times, and the ease of storing related documentation, the number of inspections and audits conducted has skyrocketed. Although the client was expecting the benefits of reduced travel, including reducing their carbon footprint, the ease of arranging the logistics of a remote inspection with SightCall has proven to be even more beneficial.
Employee and partner feedback has been incredibly positive:
“Usually these types of changes are tough to get off the ground, but after the initial rollout, the feedback was all positive, and the team was very impressed. While some were thinking this was a temporary solution, we all know now that’s not the case – now that the tool has been implemented and it’s so easy to use, we’re getting great feedback.” – Chiara Frausin Global Supplier & CoPack Data Analyst at Kraft Heinz.